Bridging with Snap Lock: A Case Study
- FlexAbility Concepts
- Nov 5, 2024
- 3 min read
Updated: Nov 6, 2024
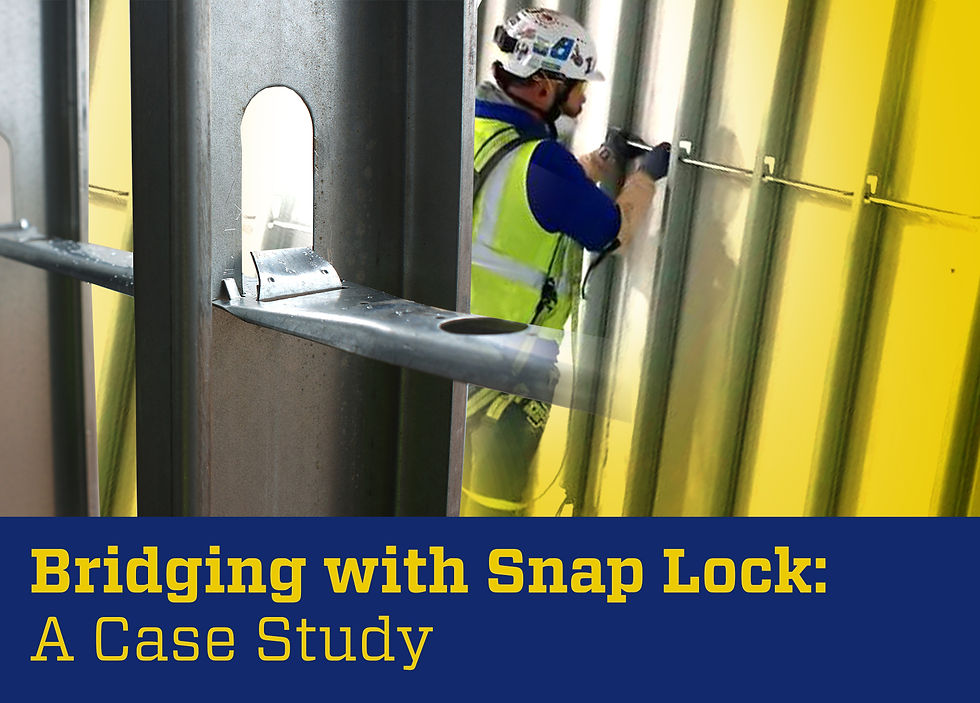
It is the nature of any business to toot its own horn. We think Snap Lock, a bridging bar, created by Flex-Ability Concepts is a way to achieve faster installations with fewer laborers. Toot toot.
Flex-Ability Concepts released its new bridge bar – Snap Lock – about one year ago. We’ve talked about the product on social media, in press releases and blogs, and at trade shows. We mention Snap Lock at face-to-face customer meetings, and we visit distributors to show off this simple device.
It never hurts to offer more education in other ways, like this case study.
Bridging and Buckling
Metal Stud bracing/bridging is the process of reinforcing the studs in a wall to prevent buckling. According to Nabil A. Rahman, writer of the article “Mechanical Bridging of Axially Loaded Cold-Formed Steel Studs,” buckling of axially loaded studs can happen in these ways:
Flexural Buckling
Torsional Buckling
Flexural-Torsional Buckling
Buckling can be prevented with the right bridging method. Snap Lock is a 16 or 24 inch bridging bar that snaps together within the knockout of the stud to provide exceptional torsional stud restraint.
Meet Baker Triangle
Starting as a small family-owned business, Baker Triangle now employs more than 1,600 employees across seven offices based in Texas as a drywall and plaster specialty contractor.
After learning about the new bridging product, Snap Lock by Flex-Ability Concepts, Baker Triangle was eager to test it out. Several discussions and meetings with Amanda Pulley, a Flex-Ability Concepts manufacturer’s representative, led to the selection of a couple of projects for Snap Lock installations.
Project 1: Subaru – Austin, Texas
About 2,400 pieces of 16-inch, 16-gauge Snap Lock were used. The height of the walls ranged from 10-30 feet. Some of the walls required two rows of bridging, while others required three rows of bridging.
Project 2: HEB – Austin, Texas
About 1,650 pieces of 16-inch, 16-gauge Snap Lock were used. The walls were more than 20 feet high, requiring three rows of bridging.
After these projects were completed, Baker Triangle compiled data and feedback, including:
Snap Lock is ideal for larger projects that have long and high walls.
Snap Lock is best to use on projects with a minimal number of openings or interruptions. This minimizes the number of start/stop instances.
Snap Lock has benefits in bays that are at least 25-feet long and have no openings.
When used in best-case scenarios, a single framer could install 700-800 feet/day on average, compared with 200-225 feet/day on average with CRC and clips.
Even in rough conditions, a single framer could average 450 feet/day.
A framer could still double their production using Snap Lock even in the worst case scenarios/rough conditions.
Snap Lock is easy to store safely on a job site, reducing the risk of being damaged or stolen.
Shawn Provencal, a superintendent with Baker Triangle, says, “We have used Snap Lock on two projects and saw an acceleration in our install schedule. Snap Lock is faster than using black iron and clips, which most drawings show for bridging. I believe we will see a 50-75% savings in labor, which would translate into installing hundreds of feet in a day. I cannot wait to use Snap Lock on a longer production wall where we can really see how fast we can install. The bigger the wall, the more labor savings that contractors can grab. Snap Lock is easier to handle from the truck, to the job site, to the location of the install. Our crew spends most of the day in a scissor lift, and we can stock the lift up with boxes of Snap Lock. This is less awkward to manage than black iron and clip, and we do not have to go up and down as often to get more material. Guys who have been with our company for 10-15 years really like working with Snap Lock.”
Baker estimated up to 75% in labor saving when using Snap Lock instead of CRC and clips. Some contributing factors included:
Faster framing meant less equipment rental time.
Fewer framers needed at a job equated to reduced labor cost.
Fewer framers also reduced the number of safety managers needed onsite, further reducing labor cost.
Baker Triangle determined that the learning curve of Snap Lock is quick and simple. On-the-job training was easy to complete and did not require any new skills. Our product representatives, like Amanda, also are available to help with training and demonstrations.
While it may be human nature for one to expound upon its talents, having another party – like Baker Triangle – present research and real-world data adds to the cause.
Are you ready to try Snap Lock?


Comments